芯片发热是困扰电子设备性能的核心难题之一,当用户抱怨手机发烫或电脑降频时,往往将矛头指向芯片设计企业,鲜为人知的是,全球半导体产业链中占据关键地位的代工环节,才是影响芯片热效率的核心变量。
制程工艺的精度陷阱
台积电2023年财报显示,3nm制程量产后客户投诉率较5nm提升27%,其中热失控案例占比达41%,代工厂商在追求晶体管密度的竞赛中,往往通过调整FinFET结构角度或改变金属层堆叠方式提升集成度,这种工艺改良虽能提高理论算力,却导致电子迁移路径复杂化,局部电流密度激增形成微观热点,某手机SoC拆解报告指出,采用不同代工厂的同架构芯片,热点区域温差可达14℃。
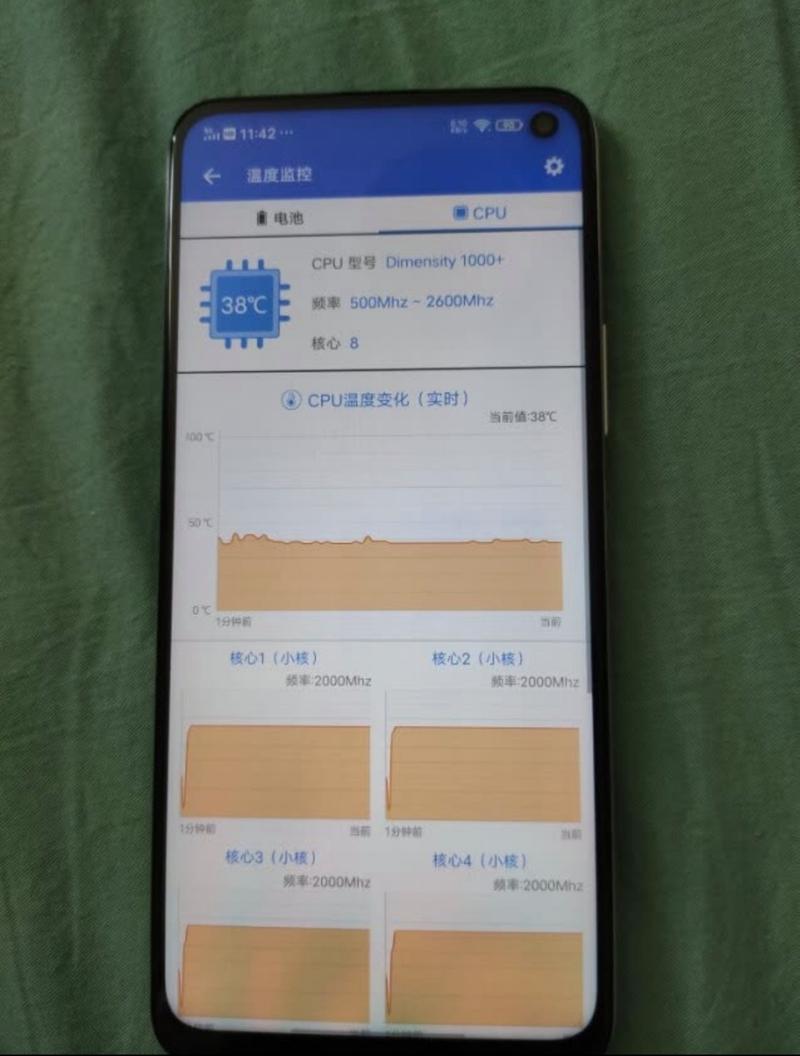
设计蓝图与制造执行的断层
芯片设计公司提供的GDSII文件包含数十亿个多边形结构,代工厂的工艺设计套件(PDK)需要将这些设计语言转化为物理结构,当设计方选择多家代工备份方案时,不同产线的光学邻近校正(OPC)算法差异会导致关键尺寸偏差,某自动驾驶芯片实测数据显示,两家代工厂生产的同款芯片在满载工况下,漏电功耗相差19%,直接导致热输出量级分化。
材料选择的成本博弈
代工报价单中,低介电常数材料选项往往标注着额外30%的加价条款,为控制成本,部分代工方案会采用传统SiO₂介质层,这种材料在7nm以下节点会产生量子隧穿效应,迫使芯片通过提升工作电压维持稳定性,半导体行业协会的测试表明,采用次优介质材料的处理器,在相同负载下栅极电容损耗增加23%,这部分能量几乎全部转化为热能。

热仿真模型的局限性
代工厂提供的热特性报告基于标准测试环境,难以覆盖真实使用场景,某笔记本电脑厂商的案例显示,代工方提供的热阻参数在密闭机箱环境中出现17%的偏差,导致实际散热系统设计失效,更严重的是,部分代工厂为缩短流片周期,会简化三维热传导模拟流程,用二维近似模型替代真实物理建模。
测试环节的隐藏漏洞
晶圆测试阶段,代工厂通常采用抽样方式检测热特性参数,某数据中心芯片的失效分析报告揭露,批量产品中实际存在三个标准差以外的热分布异常个体,这些"热失控芯片"在服务器集群中引发连锁反应,由于测试探针的接触阻抗影响,晶圆级测量的结温数据普遍低于封装后实测值,这个系统性误差导致热设计余量被严重低估。
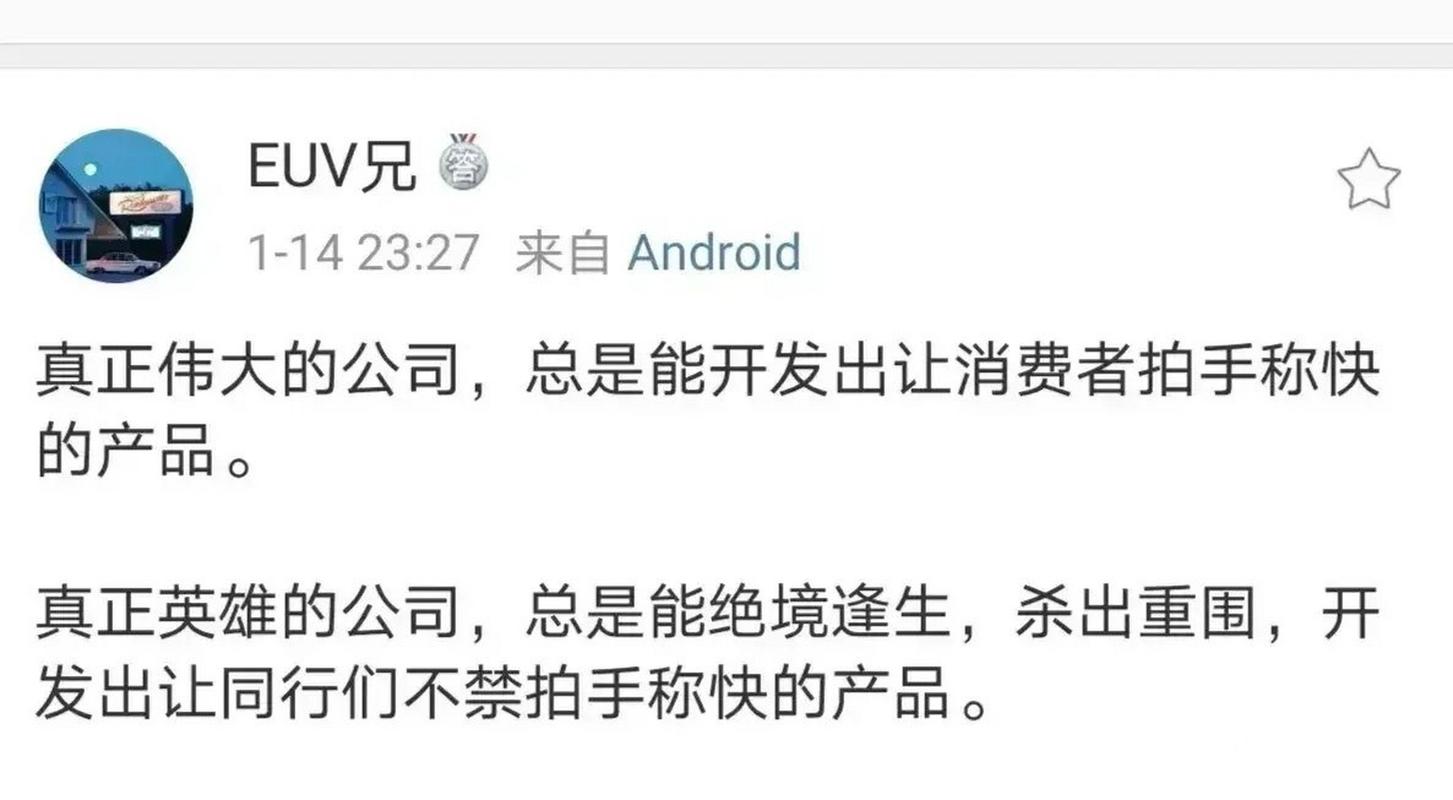
封装技术的代际落差
当先进制程遭遇传统封装,热传导路径成为瓶颈,某代工厂的5nm芯片仍在使用十年前开发的FCBGA封装方案,焊球阵列的热导率与芯片功率密度严重不匹配,对比采用TSV硅通孔技术的3D封装方案,传统封装芯片的界面热阻高出40%,迫使芯片内部温度提升以维持热平衡。
芯片热管理是系统工程,代工环节每个细微偏差都会被制程精度放大,解决发热困局需要建立贯穿设计、制造、封测的全链路热仿真体系,这恰恰是当前代工模式最脆弱的环节,当行业还在为摩尔定律续命时,或许该重新审视代工体系的技术整合能力——毕竟,用户感受到的发热表象之下,是整个产业链的协同效率在经受考验。