第一步:从三维数据到结构化信息
CAD模型本质是包含几何参数、材质属性和装配关系的三维数据集合,若要让AI理解并利用这些数据,需先完成以下预处理:
- 数据格式标准化
将不同格式的CAD文件(如DWG、STEP、IGES)转换为通用格式(如STL、OBJ),可通过AutoCAD、SolidWorks等工具导出,或使用开源库OpenCASCADE进行批量转换。 - 特征提取与标签化
利用几何算法识别模型中的关键特征:孔洞尺寸、曲面曲率、装配约束等,并通过JSON或XML格式为每个特征添加语义标签,标注“轴承座内径公差±0.01mm”可帮助AI理解设计意图。 - 构建参数关系图谱
使用图数据库(如Neo4j)建立特征间的关联规则,当电机功率提升20%时,散热片面积需增加15%”——这种逻辑链将为AI提供推理依据。
第二步:选择AI技术的适配场景
并非所有CAD数据都需“全盘AI化”,根据目标选择技术方案可显著提升效率:
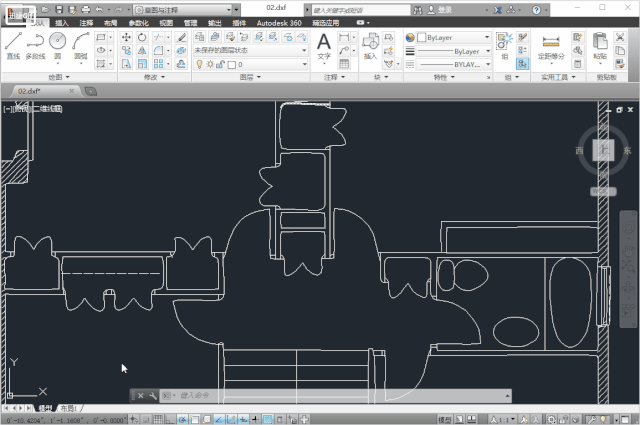
设计自动化与优化
- 生成式设计:通过GAN(生成对抗网络)或扩散模型,输入性能参数(如承重、成本),AI自动生成满足条件的结构方案,Autodesk的Generative Design工具已实现该功能,将设计周期缩短70%。
- 参数优化:利用强化学习调整CAD模型的尺寸参数,某汽车零部件企业通过AI迭代10万次,找到减重12%且强度不变的最优解。
制造缺陷预测
将CAD模型与历史生产数据结合,训练深度学习模型预测加工误差,某数控机床厂商在CAM阶段导入AI系统,提前识别刀具路径冲突,良品率提升9%。
智能运维与仿真
为CAD模型附加物理属性(如材料弹性模量、热膨胀系数),结合有限元分析(FEA)数据,训练AI模拟真实环境下的性能变化,风电企业Vestas通过该技术,将叶片寿命预测误差从15%降至3%。
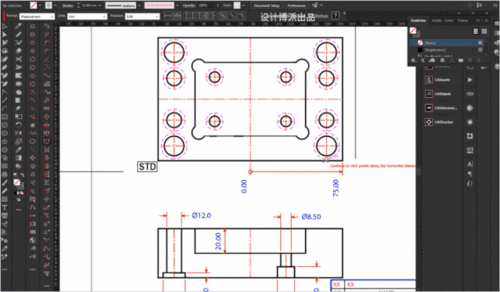
第三步:突破技术落地的关键瓶颈
从理论到实践,需解决三大挑战:
- 数据质量决定AI上限
- 案例:某消费电子公司初期直接导入未清洗的CAD数据,导致AI误将装饰性镂空结构识别为散热孔,方案错误率高达40%,后期引入人工复核机制,错误率降至5%以下。
- 建议:建立“几何检查-逻辑校验-领域专家确认”三级质检流程。
-
算法需与工程经验融合
纯数据驱动的AI容易忽略行业隐性知识,航空零件设计中“应力集中区必须避免锐角”的规则,需转化为算法约束条件,可采用混合建模:用神经网络处理数据,用符号逻辑嵌入领域规则。 -
算力资源的高效分配
训练AI模型时,过度依赖GPU集群可能导致成本失控,可通过以下方式优化:
- 对非关键特征(如表面纹理)进行轻量化处理;
- 采用迁移学习,复用已有模型参数;
- 使用AutoML工具自动选择最优超参数。
未来展望:CAD与AI的共生进化
当CAD模型从“被动存档”转变为“主动思考”的智能体,其价值将突破传统边界,想象一个场景:设计师修改某个零件孔径后,AI实时模拟下游工序影响,自动调整模具方案并推送供应商报价——这种闭环正是工业4.0的核心图景。
技术的终点始终是“人”,与其纠结CAD与AI谁主导谁,不如将其视为工程师的能力延伸,毕竟,再强大的算法也无法替代人类对创新本质的洞察。